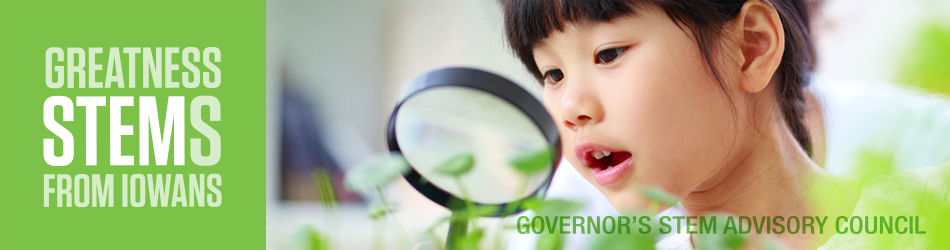
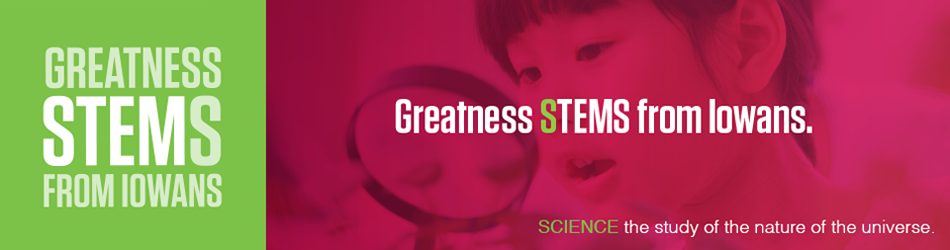
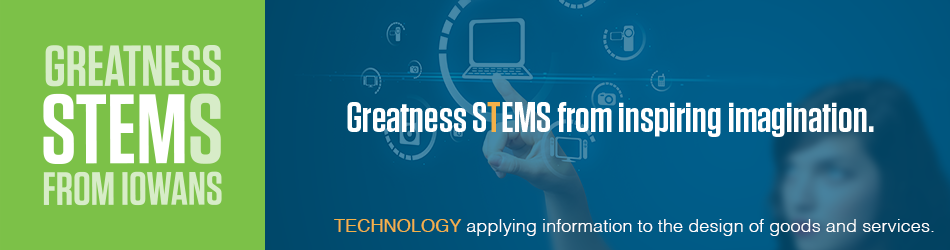
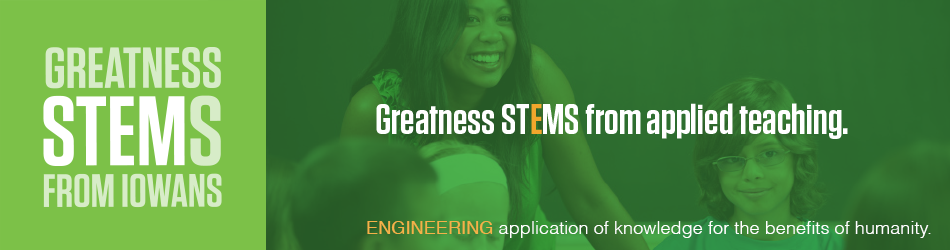
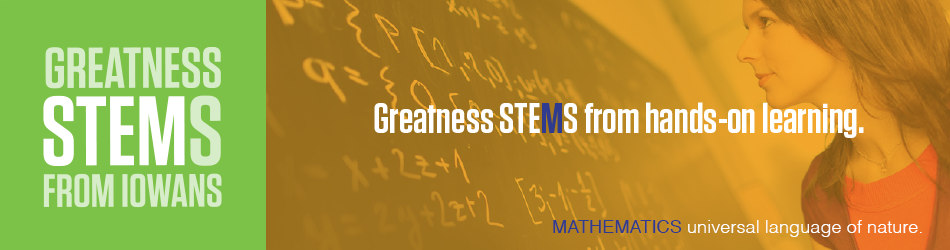
Job Information
Barilla Quality Specialist in Ames, Iowa
Quality Specialist
Job Purpose: The Audit and Quality Specialist is an integral part of the team that will help ensure the site adheres to FSMA, GFSI and partner audit requirements. This includes coordinating internal audits and GAP assessments, documenting audit reports, non-conformities, and follow-ups to ensure corrective actions are complete and effective. This role will coordinate with the cross-functional teams to ensure inspections, corrections and corrective actions are implemented and effective as well as perform administrative duties in support of site inspection readiness. This position will be responsible for ensuring site documentation is organized, current and accessible.
Key Accountabilities
Owner of the Internal Audit program – this includes preparing the internal audit plans and calendar, coordinating training of internal auditors, reviewing internal audit reports and following up with cross-functional teams on implementation of corrective actions.
Conduct internal audits such as those related to GMP/Food Safety Systems and /or GFSI benchmarked schemes like FSMA, FSSC and GAP assessments.
Participate in the food Safety and HACCP teams.
Act in place of the manager or supervisor in their absence.
Document and follow-up o post inspection/audit findings to ensure corrections and corrective actions are documented and completed.
Manage document control program for the site to ensure audit related documents and programs are up to date with regulatory requirements and best practices.
Participate, support, coordinate, and follow-up on internal meetings and or meetings with the site departments.
Provide support and assist with development of food safety culture education and activities for the site.
The individual will identify and work with the business to address food safety/quality risk, gaps and opportunities for new programs, processes, and systems.
This person plays a critical role in developing documentation, processes and programs needed such as food safety/quality risk assessments, specifications, line sampling, checks, defect standards, and training to ensure high level quality.
Provide insight and support in the development, implementation, and ongoing tracking of appropriate Quality performance KPI’s.
Drives the continuous improvement process; identifies improvement opportunities and applies appropriate tools to improve bottom-line results.
Delivers results in the areas of safety, quality, and cost.
Develops the capabilities and competencies of employees through ongoing training; promotes employee engagement, empowerment, and teamwork.
Self-discipline and organizational skills to ensure that schedule is maintained, and audits are performed correctly.
Strong interpersonal skills are necessary to discuss audit findings tactfully and objectively with plant personnel.
Strong computer skills are needed to produce analysis.
Auditing experience in food plant(s) setting is necessary to fulfill auditing business.
The ability to ensure that the audit is performed within the specified time frame and according to predetermined formats.
Must be able to work autonomously and able to deal with situations in a diplomatic and professional manner. Each audit offers its own set of unique circumstances where a problem could result.
This person determines compliance against a given set of criteria and assigns non conformances based upon such criteria.
Ability to manage multiple priorities and projects under tight timelines; works with a sense of urgency.
Detail oriented, analytical thinker and consistently demonstrates accuracy, thoroughness, and dependability.
Ability to read and understand regulatory and audit requirements.
Additional Infromation (education level, experience, competencies, equiment used, licenses, ect. in this area.)
A minimum of a BS in Food Science, Quality Assurance or a related degree such as Food Manufacturing.
A minimum of 5 years of quality assurance experience in a food-manufacturing environment is preferred.
Must have food safety management experience, preferably ISO22000 and PAS220 or ISO9001.
Required to be a FSMA qualified individual, following all requirements from FSMA regulations
Ensure compliance and understanding for quality procedures that directly tie to food safety—PRPs, OPRPs, CCPs and FSMA requirements.
Backup Gluten Free Certification Organization, or other gluten free certifications, facility contact in the event the Quality & Technology Manager is not available
Required to actively participate in mock traces, utilizing the traceability SOP, with the traceability and logistic teams. In the event of an actual trace event, actively support in all tracing activities
BENEFITS:
NO LAY OFFS since opening in 1998
Stellar safety record
10% - 13% shift differential
6% 401K match - $1 for $1 up to 6%
Tuition reimbursement
Fitness membership/wellness app reimbursement
Club membership reimbursement
Onsite fitness center
Free pasta
Annual employee bonus based on plant and employee performance
Employee referral bonus
Flexible scheduling
& so much more!
Diverse candidates and veterans encouraged to apply.
Barilla is an equal opportunity employer. It is the policy of Barilla to prohibit discrimination and harassment of any type and to afford equal employment opportunities to employees and applicants without regard characteristics including, but not limited to, age, race, color, culture, ethnicity, nationality, faith, religion, gender, pregnancy, family status, sexual orientation, gender identity and/or expression, genetic information, veteran or protected veteran status, political opinions, health or disability.